Bi-oriented polypropylene film (BOPP) has been used for decades in the flexible packaging industry. It is widely appreciated for its low cost, excellent optical and mechanical characteristics, and its outstanding gas barrier property (particularly to water vapor).
The film thickness ranges from 15 to 60 micron, and is composed of at least three layers: the middle layer is the thickest and contributes almost exclusively to the mechanical properties; the two outer layers lend various properties to the film (i.e. heat-sealing properties).
Depending on what the final application the film is intended for, additives may be added, in order to fully meet the application requirements.

1. Raw material feeding system
The main raw material, in the central layer, is the isotactic Polypropylene, a semi-crystalline and thermoplastic material. Whereas, for the outer layers, ethylene-propylene and/or ethylene-butane-propylene copolymers are used. These materials are introduced inside the extruders by a hopper system.
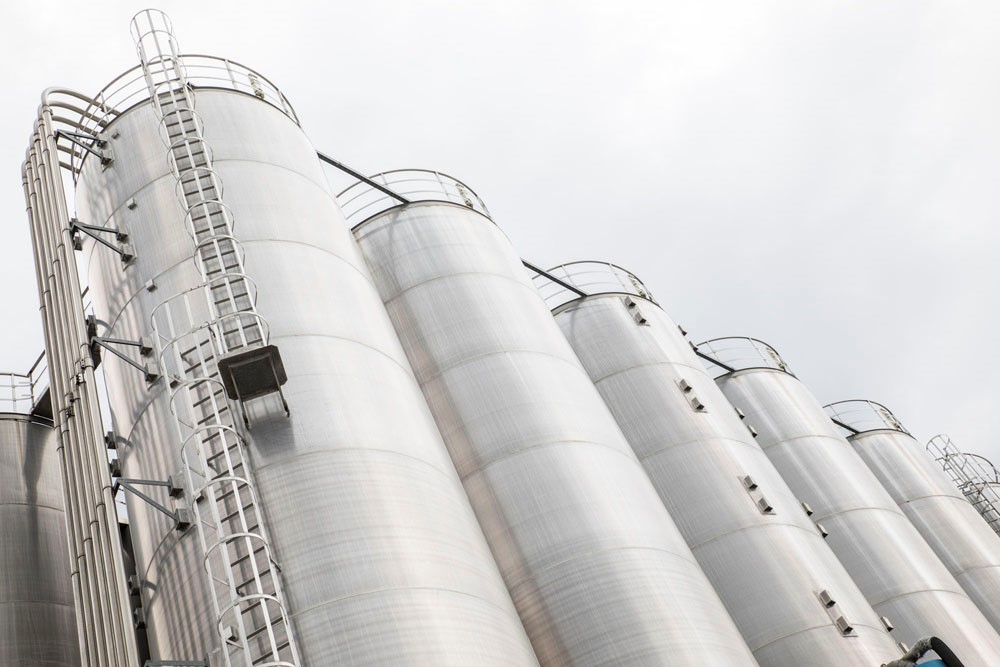
2. Extrusion
Inside the extruders, the materials are melted and brought to 200-230°C and then conveyed through the extrusion head, where they emerge in the form of foil.
3. The foil cooling
The foil is then placed in direct contact with a cooled cylinder and immersed in a water bath to quench the melt.
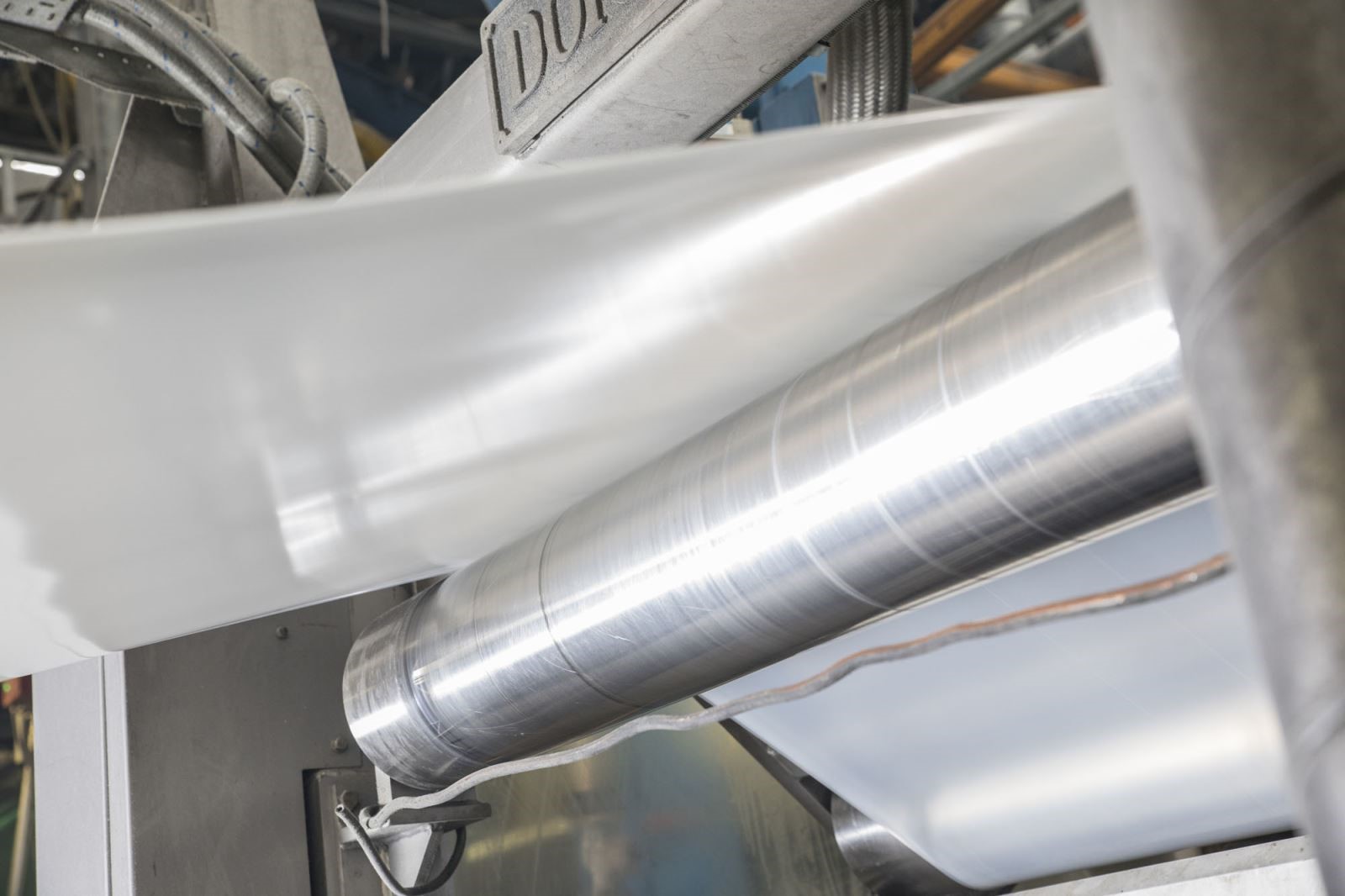
4. Machine direction orientation (MDO)
The film then passes over a series of rollers, which increase the temperature and prearrange it to stretch longitudinally (machine direction). The stretching is achieved by passing the foil between the rollers that run at increasing speeds. As a rule, the foil is stretched up to five times the initial length and, at this stage the polymer chains are aligned. This stage allows the enhancing of the film's mechanical properties, also, the thickness is reduced up to five times.
After stretching, the film is heated once again in order to neutralize the stress accumulated during the stretching (annealing phase).
5. Transverse direction orientation (TDO)
Once out of the longitudinal stretching zone, the film is gripped on both edges by a fast-moving chain of metal jaws (tenter clips). In the tenter, the film goes into an oven, where its temperature rises before being stretched transversely by the diverging rails (i.e. stretching in transverse direction up to 9 times its original width).
At this stage, the macromolecules align, this time in transverse direction, enhancing the film mechanical properties and reducing the thickness up to 9 times. Following the stretching stage, the chain and the film converge , so that the film neutralizes the stress accumulated during the stretching (annealing phase).
6. Thickness measurement and flame treatment
The film reaches a new processing stage where it takes the automatic measurement of the thickness (along the entire width).
Afterwards, one of the faces is subject to the flame or corona treatment to make the film suitable for the following conversion activities, namely, modifying the surface, that is intended to anchor materials such as ink (printing process), adhesive (lamination process), or metal (metallization process).
7. Reel winding
The film is wrapped around a reel and is slit according to the requested dimensions.
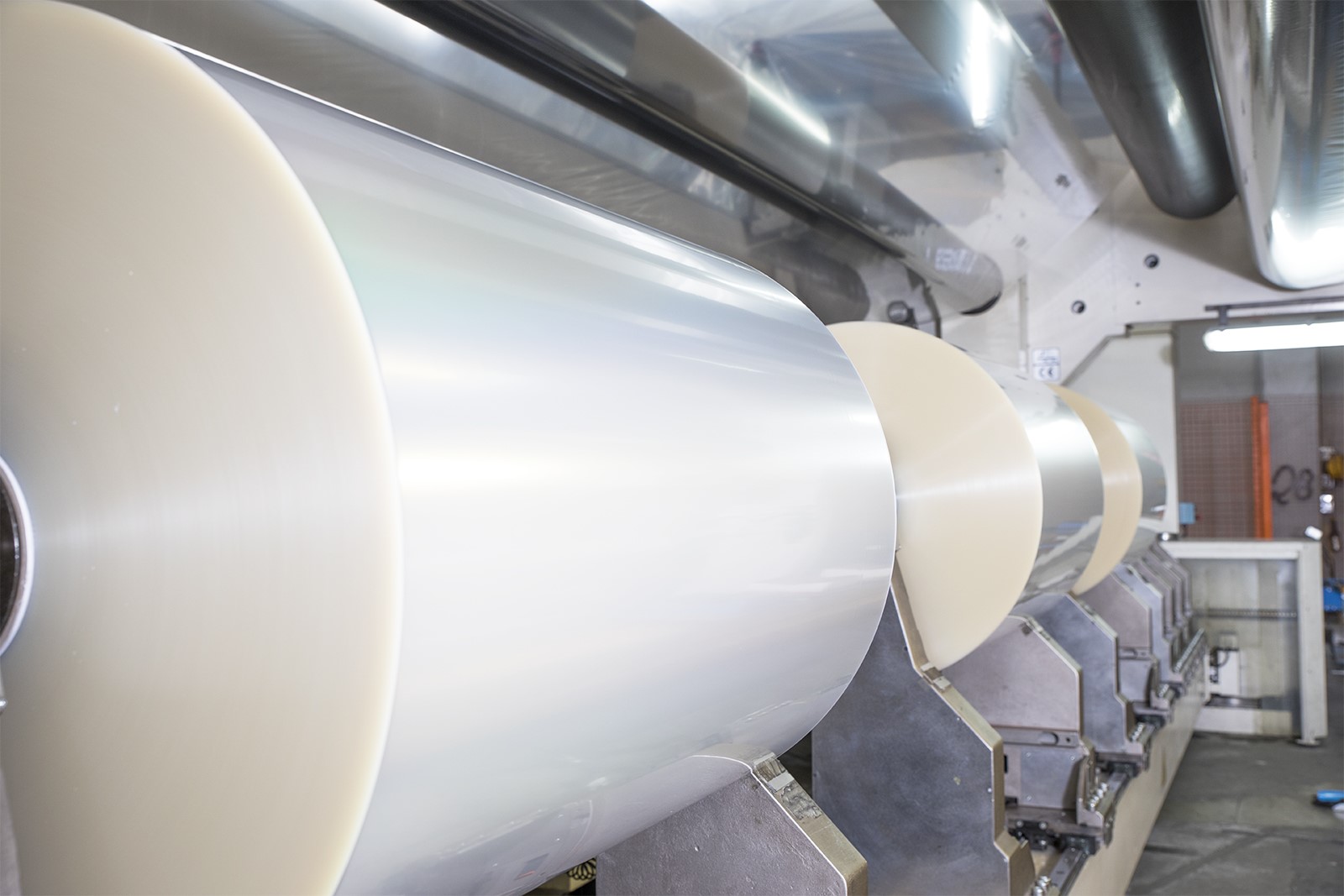